Our method – standardisation
Consistency through standardisation
Bedrocan is the only company in the world that has the proven capability of producing standardised cannabis flos (whole, dried flower). Through a combination of stable plant genetics, automated, high-tech production techniques, Bedrocan has the capacity to grow varieties containing consistent levels of cannabinoids, every time.
Moreover, we are the first medicinal cannabis producer in the world to produce medicinal cannabis according to the EU guidelines for good manufacturing practice (GMP).
Why should you care about standardisation?
For one, it’s not just about stable THC and CBD content from one batch to another. It is also about balancing over one hundred potential active components, from cannabinoids to terpenes.
Standardisation is the only method of ensuring that prescribers and patients can achieve a consistent therapeutic effect over time.
Standardisation helps assure dosage composition, the repeatability of dose, and greater ability for patients and prescribers to adjust dose by titration. This allows for proper monitoring of the product’s efficacy, safety and potential side effects.
Standardisation enables the comparison of findings from different clinical trials and studies across time. It is a critical factor for building the evidence-base of for the efficacy medicinal cannabis.
No milling and blending
A level of standardisation may be achieved by milling and blending varieties with different cannabinoid content. However, this process only creates equal levels of one or two target compounds (typically THC and/or CBD) – not the entire cannabinoid and terpene profile. By comparison, Bedrocan cannabis flos has a consistent cannabinoid and terpene profile, meaning it is produced to the same rigour as traditional prescription medicines.
The world’s most advanced production facilities
Bedrocan’s production facilities incorporates the proprietary design, software and standardised production techniques developed over decades of cultivation experience in the Netherlands.
Our indoor growing rooms use state-of-the-art environmental control technologies to control all variables, including light, temperature, nutrients, and water. Each of these rooms is sealed with special doors to prevent contact with airborne contaminants. Our production process has been specifically refined to grow standardised cannabis flos without the use of any pesticides. In addition, our international quality assurance measures are proudly achieved with very high hygiene standards, relevant testing requirements, and strict pesticide and fungicide restrictions.
Every week a fresh batch can be harvested, 52 weeks per year, to a schedule we can predict years in advance.
Behind-the-scenes
Bedrocan has been visited several times by television makers:
- Reizen Weas, the well-known Belgian travel program presented by Tom Waes
- Discovery Channel’s How Do They Do It? presented by Joep van Deudekom
Curious about the behind-the-scenes video’s at Bedrocan? Watch the episode of Reizen Waes or How Do They Do It. Click on one of the buttons below.
Cultivation of standardised varieties
Each of our varieties are bred to meet the different and changing needs of patients who require access to multiple standardised varieties, with different cannabinoid and terpene profiles.
Each cultivar originates from one single seed. Our plants are grown by multiplying the original plant material. Bedrocan uses proprietary vegetative propagation techniques to give our products remarkable genetic stability. This method prevents ‘genetic drift’, a problem resulting from repeated vegetative propagation of the mother plants, which can cause major changes and weakness in the plant over time.
Bedrocan takes the science of cannabis cultivation very seriously. We have developed unique, proprietary processes which bring unparalleled precision to cannabis production. During the entire growth process and processing we dedicate ourselves to ensuring that the cannabinoid (THC, CBD) levels are constant and that no harmful microorganisms find their way in to the end product. Each batch is checked to confirm it meets the required levels of essential components (THC, CBD). These tests are required by government regulators and conducted by independent laboratories. Once the certificate of analysis are delivered, the medicinal cannabis can be released for delivery to pharmacies, researchers and industry worldwide.
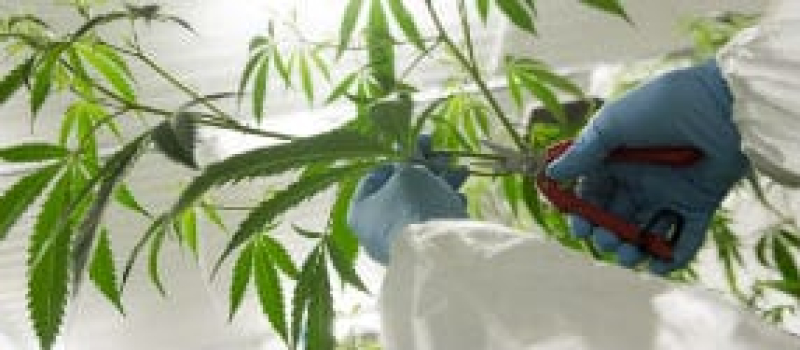
A cutting is obtained
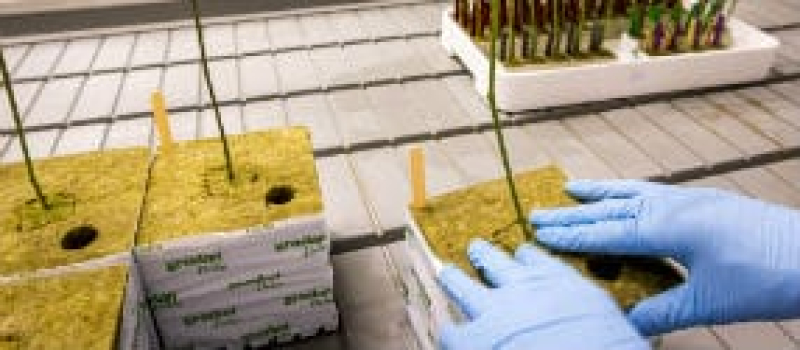
Plants are placed into Rockwool
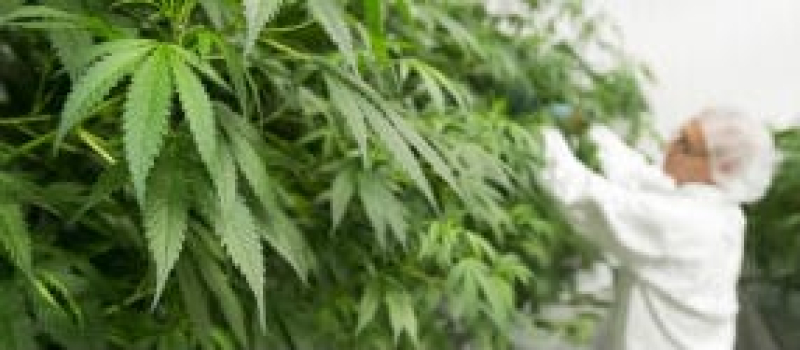
The plants are placed in a growing room
Drying, processing and packaging
Drying, processing and packaging takes place in a separate, specialised compartment of our cultivation facilities. After the cannabis is dried the flowers are manicured. This trimming process is undertaken manually, as it guarantees an extra visual quality control. This method also protects the trichomes; the fine outgrowths of the cannabis plant containing the important active constituents.
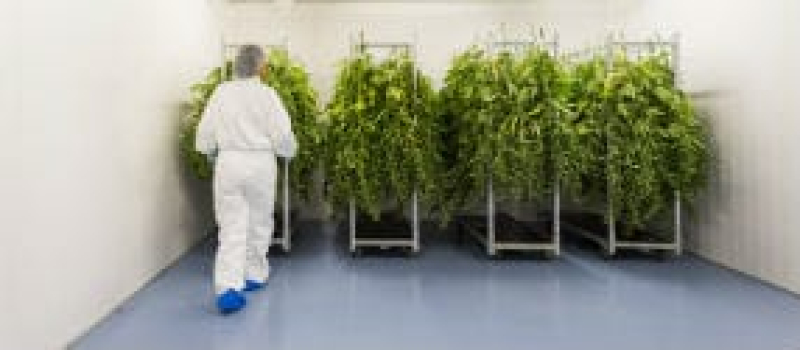
The harvested cannabis plant is dried
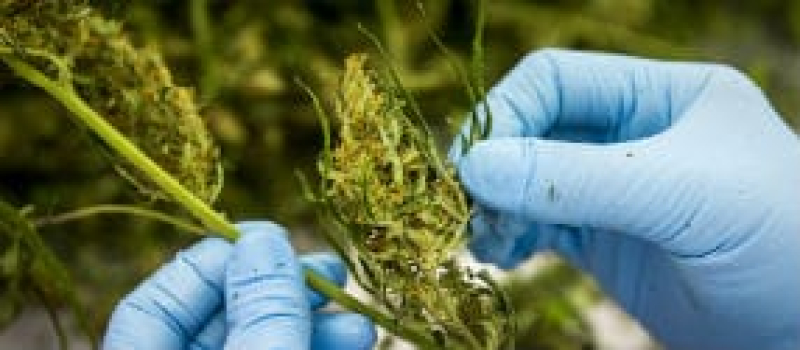
The stems and leaves are removed
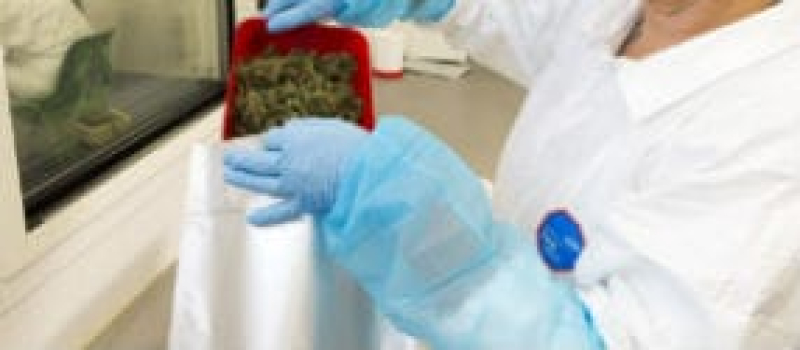
The cannabis flos is packaged
All products are exposed to gamma irradiation to eliminate objectionable microorganisms, like fungi and bacteria. Gamma irradiation has been shown not to affect the quality of cannabis flos. This process ensures the cannabis flos is safe for vaporization and inhalation by immune-compromised patients.
No pesticides or heavy metals
The cannabis plant can quickly take up heavy metals. Therefore every batch is individually sampled and checked for the presence of heavy metals as specified in the Dutch monograph. Regardless, each batch is also tested for the absence of pesticides, even though we do not use pesticides in our production process at any time.